* »óǰ°¡°Ý ¹× Àç°í ¹®ÀÇ : https://hankookceratec.co.kr/html/5_1.php
[Order Information]
* Standard Epoxy (¹Í½Ì ¹«°Ôºñ R 11 : H2)
EP-3000-32P : EPOCAST Epoxy Plus Resin (1Liter)
EH-3000-08P : EPOCAST Epoxy Plus Hardener (250ml)
* Quick Mount Epoxy (¹Í½Ì ¹«°Ôºñ R 10 : H1)
ERF-3000-32 : QUICKMOUNT 2 Fast Epoxy Resin (1Liter)
EHF-3000-08 : QUICKMOUNT 2 Fast Epoxy Hardener (250ml)
* Low Viscosity Epoxy (¹Í½Ì ¹«°Ôºñ R 10 : H1)
ULTRA-3000R-32 : ULTRATHIN 2 Low Viscosity Epoxy Resin (1Liter)
ULTRA-3000H-08 : ULTRATHIN 2 Low Viscosity Epoxy Hardener (250ml)
CASTABLE RESIN PROPERTIES |
¡¡ | EPOXY | ACRYLIC | POLYSTER Resin |
Type | Epoxy resin and hardener | Acrylic resin
and powder | Polyester resin
and hardener |
peak Temperature | 38~190oC | 65oC | 38oC |
Shore D Hardness | 82 | 80 | 76 |
Cure Time | 30
minutes to 8 hours | 5-8 minutes | 6-8
hours |
Comments | Moderate
hardness, low shrinkage, transparent | Very
fast cure, translucent, some shrinkage | Transparent,
water clear |
Epoxy Resins The most common and best performing castable resins are epoxy based (Figure 4-2).
Epoxy resins are typically two-part systems consisting of a resin and a catalyst (hardener).
Mixing ratio's vary from ten parts resin with one part hardener to five parts resin with one part by weight of hardener.
The advantages of mounting with epoxy resins include:

- Low shrinkage
- Relatively clear
- Relatively low exotherms
- Excellent adhesion
- Excellent chemical resistance
- Good hardness
- Relatively inexpensive
Epoxy curing times are dependent upon a number of variables including:
- Volume of mounting resin (larger mounts cure faster).
- Thermal mass of specimen (larger specimens absorb heat and therefore require longer curing time).
- Specimen material properties.
- Initial resin temperature (higher temperatures cure faster).
- Ambient temperature (higher temperatures cure faster).
- Relative humidity and shelf life (absorption of water degrades resin and shortens shelf life).
- Mounting mold (plastic, phenolic rings, rubber absorb heat differently).
As a general rule, curing times can vary from 30-45 minutes for fast curing epoxies up to 24 hours for slower curing epoxies.
For metallographic epoxies to grind properly, the hardness needs to be at least a Shore D80.
Note that epoxy resins typically will continue to harden over a longer period of time (maximum hardness, Shore D90).
In some cases, the curing time and temperature may need to be controlled to compensate for the above variables.
For example, an 8-hour resin system can be cured in 30-45 minutes by preheating the resin to approximately 120¡ÆF (50¡ÆC) prior to mixing
and then curing at room temperature.
This procedure initiates the catalytic reaction sooner; however, this may also increase the maximum exotherm temperature.
TIP: Preheat the specimen to initiate the epoxy resin at the surface of the mount
and thus have the epoxy shrink towards the sample for better edge retention.
Conversely, the resin curing cycle can be slowed
or reduced by decreasing the curing temperature by forcing air over the curing mounts (fume hood or fan),
placing the mounts into a water bath, or curing in a refrigerator.
In these cases, care must be taken to not stop the reaction; however if this does occur or the resin is too soft after curing,
heating it to 100-120¡ÆF for several hours should push the reaction to completion and the mount should be hard after cooling to room temperature.
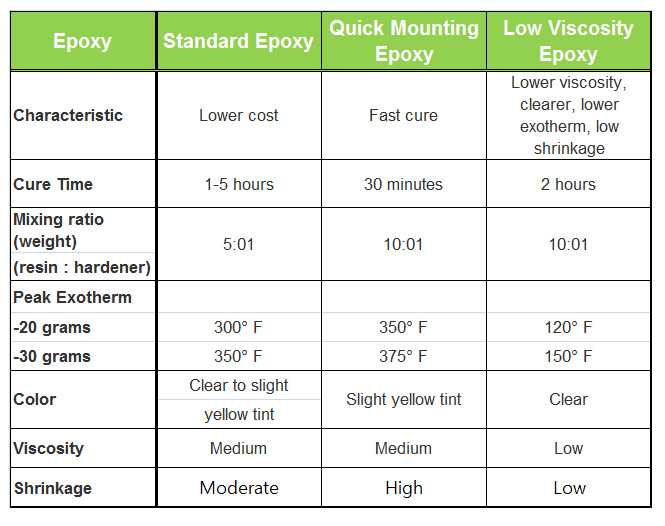